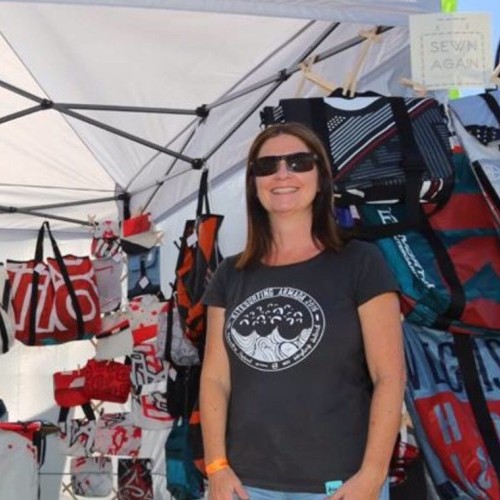
The Fabric of Kitesurfing History – Louise Hadlow
Features / Tue 4th Oct, 2022 @ 6:00 pm
The Hadlow name is, unquestionably, one of the most recognisable in the world of kiteboarding. When you hear Hadlow, it’s likely 5X world champion and 2X Red Bull King of the Air winner Aaron Hadlow that comes to mind. However, this feature is not about Aaron, it’s about another very special Hadlow!
Louise Hadlow, Aaron’s mum, runs a company called Sewn Again, and Ryan Mizzen, a long-time supporter of her company, wrote in to IKSURFMAG to share:
“This past September, the annual Kitesurfing Armada festival was set to return to Hayling Island in the UK, which should have been one of the highlights in the kitesurfing calendar. Unfortunately, the event was cancelled, which, for those who’ve keenly awaited the event, was a big disappointment. But, for some exhibitors, months of hard work have gone into preparation for the event. One of those exhibitors was Louise Hadlow, who runs my personal favourite stand at the Armada.
Louise is a very talented seamstress, who had a brilliant idea to help avoid used kites being sent to landfill. She now upcycles Aaron Hadlow’s used kites by turning them into an incredible selection of one of a kind bags. These include backpacks, beach bags, laptop bags, handbags, holdalls, dog walking bags, phone bags, sling bags, chalk bags, rucksacks, toiletry bags, and shopping bags, amongst a wider selection, which occasionally includes a teddy bear!
These strong, versatile and eye-catching bags generate a ton of interest at the Armada and Louise’s stall is packed on the first day, but almost entirely sold out by the last day of the festival. These bags aren’t just special because they’re unique, they’re sought after because they’re part of the fabric of kitesurfing history.”
To find out a bit more about Louse, her business, and her background, Crystal Veness caught up with Louise Hadlow in this Q&A:
Louise, what inspired you to upcycle old kites into functional items?
The spark that ignited my journey into recycling Aaron’s old kites into functional bags, arose from two key factors. The first being when Aaron changed his sponsorship to a new brand. The second factor came about when we were moving house.
Aaron had a long history with Flexifoil and over the course of many years we’d accumulated old, broken and prototype kites. All of which ended up being stored in our garage. Whilst sorting through the kites trying to decide how to dispose of them, we quickly came to realise that we couldn’t just destroy them and waste all that expensive material – we couldn’t just send them to landfill. We eventually thought about transforming them into bags even though I’d never made one before!
What is it like working with kite material? Are there challenges using this sort of material in a sewing machine?
There are two types of material that are used to make kites. One is RipStop (the thinner material, which forms the main part of the canopy) and the other is Dacron (the thicker material, from the leading edge, struts and tips). Both offer challenges when making kite bags.
The RipStop is very slippery to work with and doesn’t grip the small feed teeth that push it through the sewing machine, so trying to keep a straight seam in the early days was a real challenge. Working with the Dacron is even more difficult. It’s tough material with no give, which is even more slippery, and doesn’t want to be folded. So working with both these materials was a real learning curve.
Do you have to use any special techniques, needle, or thread, to create long-lasting products?
I soon realised I needed to invest in some specialised sewing feet for the sewing machine. This is because I had to get the kite material to feed through the machine evenly, which seemed to be the key to sewing with these two materials.
Experimenting with different size needles and strong threads also made a difference. Eventually through trial and error all these changes made it easier, but the biggest game changer came when I invested in a stronger more powerful sewing machine. Finally, everything aligned and the sewing and finishing of each bag improved greatly.
What was the first product you created?
The first bags I made were some messenger bags. The outside of the bags were made from Dacron and I lined them with RipStop. I didn’t use a pattern; I just made a trial bag of how I thought it should be constructed and went with it. I then ended up making nine.
What is your most in-demand item on the website?
The second bag we thought about creating was the Large Beach/Kit bag. We wanted a bag that was big enough to put your bar, harness, pump, and wetsuit in, so that when walking down the beach you don’t keep dropping pieces of equipment. Trying to balance all these items along with your boards and kites is always a mission, especially if you have a long walk. What we didn’t realise at the time was that this bag was going to be my best-selling bag.
Are there any new designs that you’re dreaming up that fans of your work can look forward to?
I’m constantly looking at bags in shops, on the internet, out and about, on the beach, in cafes and just about anywhere else I go. I buy most of my patterns now as they have got more complicated and intricate over the years.
Recently I’ve spotted a couple of fold-up bag ideas; one is a backpack and the other is a barrel bag. I like the fact you can keep them flat-packed and take them anywhere. I’m quite keen to have a go at making these and see how they turn out. I like to make bags that are useful and practical; bags that will actually get used, as that’s really the whole idea behind recycling and up-cycling.
Is it sometimes an emotional experience working with equipment that your son has ridden to achieve special milestones in his career? Is there a kite you’ve taken apart that had an especially meaningful story behind it?
All the kites that Aaron has used over the 20+ years are special, because of the memories they’ve created along the way and the milestones they have marked in Aaron’s career. One of my favourites was the old Flexifoil Storm (they had some lightning bolts and turtles on them, which make nice details on the bags). I remember Aaron had a photoshoot in Shark Bay on this kite, and it was a beautiful sunny location.
Then, more recently, the Duotone (old North) pale blue kites with all the Red Bull logos on them were also a great favourite of mine. But, any with the Hadlow logo are still my favourites, as seeing Aaron’s name on the kites makes me immensely proud.
It’s amazing what you as an individual are doing to recycle and epicycle products that would typically go to waste. What do you think the kiteboarding industry as a whole can do to achieve more sustainable business practices?
I think we have all got into the habit of recycling what we can. We’ve all got better at this and that’s good to see. There also seems to be a big shift with kite companies changing the way they package and ship their products, by using recycled cardboard and plastic components, which is great as you can pop these into the recycle bin.
With the new technologies and chemical compounds being explored and invented, hopefully soon all boards and kite materials will be made in an eco-friendly way, so that when they are disposed of they will break down over the years, fading away and not leaving a trace.
You can check out more kite creations from Louise on Instagram at https://www.instagram.com/sewnagainkitebags/
By Crystal Veness
Editor at IKSURFMAG, Crystal Veness hails from Canada but is based in South Africa. When she isn't busy kitesurfing or reporting on the latest industry news for the mag, she is kicking back somewhere at a windy kite beach or working on creative media projects.