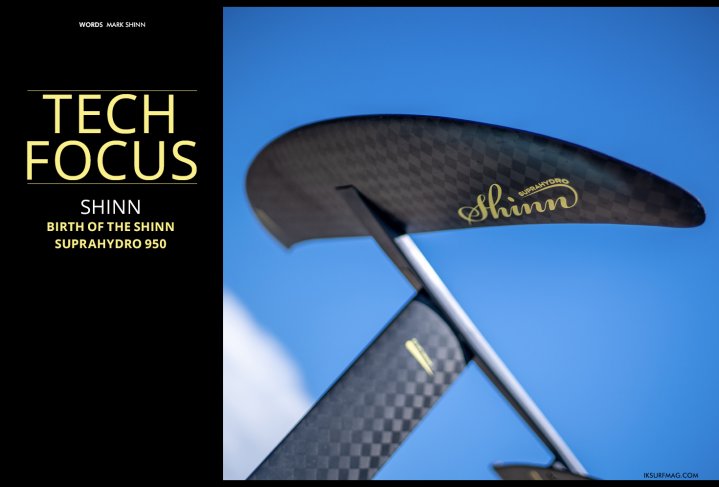
Tech Focus - Shinn Suprahydro 950
Issue 86 / Tue 13th Apr, 2021
What does the journey of a hydrofoil look like? From the sparkle in the eye of Mark Shinn to a prototype and then eventually to the market, Mark tells us how the Shinn Suprahydro 950 came to be. Read all about it right here!
Research and Development is a process. Sometimes it’s exploratory with an innovative idea, and sometimes it’s evolutionary - either the natural development of an existing product or fulfilling a demand that the current range is not satisfying. In the case of the Shinn Suprahydro 950, it was a natural expansion of our range. Our line-up already offers multisport applications, but developing a front wing of this size would give us further options by delivering a set-up for stronger wind winging, tow-in surfing, and kite-foiling.
When we have an idea of the wing’s size and desired performance range, the first step is to develop a model. Knowing we would utilise the already existing fuselage, mast, and stabiliser from the range simplifies the process and reduces the modelling time needed. Anhedral, Outline and Profile need to be established and defined, and this I do in a 2D environment before passing the information to the draftsmen to create the fully digital 3D model.
Creating the model often raises un-foreseen complications, especially when preparing the fuselage mounting area, but, once done, we can run a series of simulations and tests before moving onto the expensive and time-consuming process of creating physical prototypes. Understanding the results from simulations is not an easy task, but with each development, we learn more. With the continual application of that knowledge, we hope to one day be able to accurately predict a hydrofoil’s performance without physically making it.
Once we have the approved 3D model, we can move onto the prototyping stage. Unfortunately, having the model is still a long way from being ready to mill. CNC milling is reductive technology, meaning you are cutting away from a larger piece of material to leave behind what you want to create. Whilst the world of Additive Manufacturing (3D printing and similar techniques) is a fast-developing process, there is no way to cost-effectively 3D print a part that falls inside the required weight/strength parameters.
We produce temporary moulds for all our foils - a mould that can be used to produce 4 or 5 wings before it is destroyed. The first task is to create the drawings of the moulds. Once done, we can convert this into cutting paths and loaded to the machine to cut the moulds – a process that can take between 8 and 16 hours depending on the size of the part to be created.
Having a finished set of moulds allows the laminators to take over, and several days after we start the process, we arrive at the exciting part: We have a physical wing in our hands, and it’s over to the testers to do their thing!
There is no doubt that testing is one of the more enjoyable parts of the process. As we design and create more foils, there are fewer surprises, but until you ride it, there is always a small question mark over whether it will work. I’m still relieved when a new foil actually flies for the first time!
There is a lot of basic set up work to be done on a new foil. Stabiliser size and Angle of Incidence, Wing AOI, foil position on the board… They all contribute to the feel and performance. I always do this initial testing, but once I’m happy the foil is performing within the desired spectrum, we send it to our team of testers of varying ability levels, to test the gear on the water as much as possible.
One of the benefits of using the temporary moulds is that we can produce 4 or 5 identical prototypes, so the testing phase can go much faster. In the case of the Suprahydro 950, we went through 4 variations before we arrived at the combination of features we were searching for. From a kiteboarding perspective, this foil needs to be early starting, stable, fast enough to be fun, and above all, offer a carving performance far above anything we have done before. In these aspects, I think we have been successful.
Once approved for serial production, the product passes from the R and D team to the logistics team to prepare production moulds, graphics, marketing material, and photoshoots. It’s a long journey from having an approved prototype to getting products out there in the shops!
The Suprahydro 950 will be available in shops mid-April.
By Mark Shinn